Up until the 1990s, military rifles were rather simplistic. A basic rifle, a parade sling and, for some, an underslung M203 Grenade Launcher. Around that time, we also got smarter. We learned that red dot sights (RDS) permitted us to get faster, more accurate hits. The problem with this was the difficulty of attaching the optic to the rifle.
When U.S. Special Forces raided the Son Tay POW camp in 1970, the Armson OEG RDS were attached by field-expedient methods, including tape. The lessons observed from that great raid led others to learn from it. And while the military is large, ponderous and stifled by institutional inertia, some within (and outside) the military forged ahead.
On the civilian side of the house, hunters and target shooters had used telescopes on their rifles for years. These optics were mounted on rings that were screwed directly into the receiver. Not bad, but two separately mounted rings presented their own set of problems.
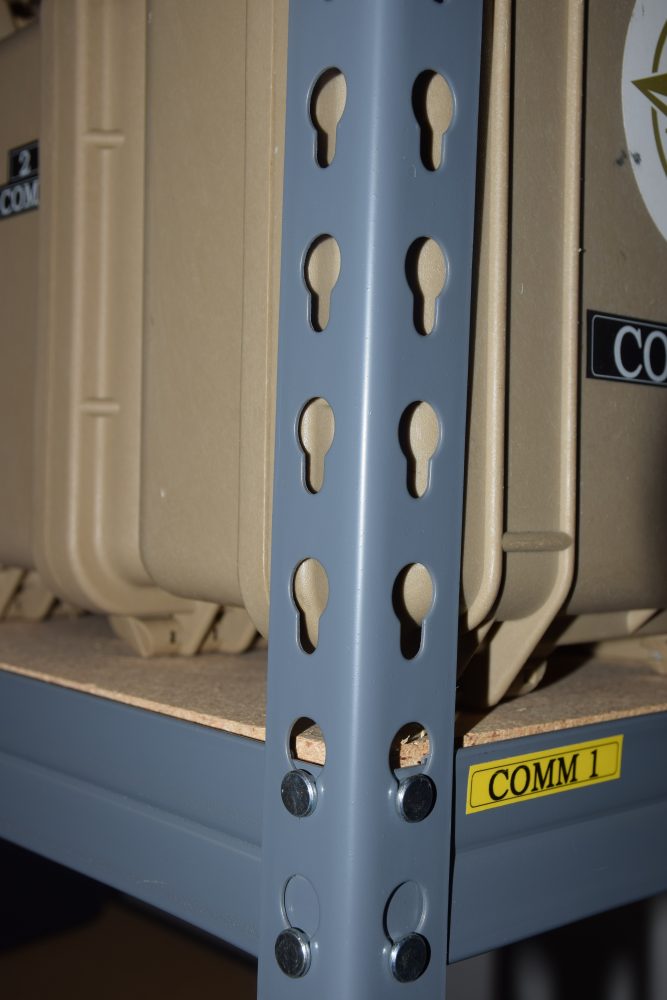
Table of Contents
WEAVER RAIL AND PICATINNY RAIL
W.R. Weaver Company developed the first standard mounting device for optics on firearms: the Weaver Rail. This was screwed into the receiver, and the optic could be mounted to the rail, which allowed for some latitude in mounting optics. Understanding that while hunting rifles are relatively strong and hunting optics a lot less fragile now than in the past, they still pale in comparison to military weapons. An additional issue is that the Weaver Rail was made to a loose standard, which would be intolerable for mil use.
The engineers at Picatinny Arsenal developed the Accessory Mounting Rail for Small Arms Weapons, whose dimensions are set in the MIL-STD-1913. This is now commonly known as the Picatinny Rail or Pic Rail, and it has remained the standard since its adoption in 1995, and will likely continue to remain so for a long time.
The Pic Rail is similar to the Weaver Rail but differs in several dimensions, as well as being consistent in manufacturing (the so-called milspec). The Pic Rail is at this time the optimal rail for return-to-zero optics. Of course the wild card is if the weapons mount itself truly conforms to the MIL-STD-1913 rail. In the mid-1990s, the Pic Rail made its military debut in the Special Operations Peculiar Modification (SOPMOD) kit with the Knights Armament Company (KAC) when they included the Rail Interface System (RIS) and the later Rail Adopter System (RAS).
QUAD RAILS
The RIS and RAS were the so-called Quad Rails; that is, there were four Picatinny rails that ran the full seven-inch length of the rail, at 12, 3, 6 and 9 o’clock. Any item that was compatible could be attached at a user-selected location to maximize efficiency.
The RIS/RAS came with rail covers, ostensibly to protect the Pic Rails from being damaged during use. However, they also protect the shooter’s hands from heat during a harsh firing schedule. And they get bonus points for preventing the shooter’s hands getting scraped up along those aluminum cheese graters.
The Quad Rail was a major step forward, epitomized by makers such as LaRue and others, and it is still a very viable platform. But some felt that there was no reason to have unnecessary rails that were adding weight and taking up space.
There are 1913 rail sections that have a KeyMod nut, which will act as an interface between the KMR and an accessory that is meant to attach to a 1913 rail. BCMGUNFIGHTER Vertical Grip is attached directly to a nine-inch KMR.
The result was a group of low-profile tubular handguards that had a means to attach small sections of Pic Rail where the shooter wanted them, and kept the rest of the rail clean. These handguards became very popular as they were light, slender and without unnecessary rail sections. Let’s face it, exposed rail sections are known as cheese graters for a reason.
The separate Picatinny Rail sections come in different lengths and add little in weight, but they do slightly increase the bulk. To a certain extent, they also limit the location where you can mount mission-essential equipment.
Ten-inch KMR rail on AR pistol. This gun has an 11.5-inch barrel—the shortest reliable barrel for direct-impingement gas systems.
KEY SLOT HANDGUARD
The slotted key attachment system has been around for 100 years or so. Anyone who has a steel shelf in the garage or industrial shelving at work has seen this type of system. The genesis for the weapons application comes from Eric Kincel, then founder of VLTOR. Eric had been working on a Marine Corps Systems Command (MARCORSYSCOM) request for a collapsible stock system for the M16 rifle, which developed into the A5 enhanced buffer system.
This led to the VLTOR CASV Handguard, which was followed by an RFP (request for proposal) in 2011 for the next evolution of the A5 system—the A5 KM (KeyMod) upper. This upper improved cooling, lowered weight, and eliminated costly mounting points. In October 2011, Eric Kincel and the late John Noveske conferred about handguards. The Noveske team was working on a bow tie design (think of the star-and-bar U.S. military insignia on aircraft), but they saw the benefit to the KeyMod slot.
VLTOR took Noveske’s drawings of the bow tie and remodeled it for the KeyMod, presenting it on 8 October 2011. Todd Krawczyk from Noveske suggested an improvement for the accessory lock/anti-rotation unit, which was adopted. By 26 October 2011, VLTOR had transmitted the first Key Slot Configuration to Noveske, and started the ball rolling.
The KeyMod is not new, but apparently many people think so…
Because of KMR’s design, barrel nut and mounting assembly weigh only 2.5 ounces.
The speed and professionalism at which this exchange transpired is refreshing, and a model for what should be going on in this industry. Eric decided (and with the permission of VLTOR’s President, Gary Abrams of Abrams Airborne) to release the Technical Data Package (TDP) to the public, with no strings attached. This ensures the community will have the proper drawings in order to maintain a standard that can be utilized efficiently by everyone.
There are a great number of people who have seen the need to have a better mousetrap, but there are also a great number of lesser people producing garbage for the sake of making money. They do a pretty good job of deselecting themselves, but in the interim it creates a plethora of items that have a various degree of usefulness. The thought process here was that with the TDP available to everyone, some degree of standardization might occur.
Combination of an Extreme Lightweight Barrel and a very light KeyMod Rail puts weight to the rear and makes the gun a lot easier to drive.
BCM KEYMOD RAIL
Which brings us up to the BCMGUNFIGHTER KeyMod Rail (KMR). In January 2013, Eric Kincel went to work for Bravo Company Mfg as Director of Research and Development. President of BCM Paul Buffoni noted the swift progress of the KeyMod’s evolution, and told Eric to make the best KeyMod Rail available.
The BCM KMR is unique for two reasons. The first is the barrel nut. Kincel had wanted to change the way the handguard was bolted to the barrel. Commonly it was clamped at the bottom (like a hose clamp) or on the sides with two halves (like a telescope mount). He felt they all had a problem as to the arch that went up and over the gas tube. It expands and loosens after the material is heated, and aluminum has an expansion rate of three to one over steel.
The KMR has two cross-bolts that travel through the gas tube and the barrel nut. This eliminates the expanding arch and, as less force is needed to clamp the rail to the barrel nut, the hardware could be lighter than on conventional barrel nuts. Because the barrel nut is so small, he made the interface of the barrel nut the same as the M4 receiver extension lock nut (the so-called castle nut). This means that if you don’t have a BCM barrel wrench, you can use your castle nut wrench.
Lastly, the index plate is a simple metal stamping that spreads around the lower portion of the Pic Rail, but at the same time expands inside the KMR. This ensures a tight fit and proper index of all mating components.
Jace Badia with Bravo Company Mfg 13-inch KMR. Jace is one of hardest guys author has ever met.
UNIQUE MATERIAL
The second is the material used. Railed handguards are normally made of aluminum, which strikes a compromise between weight and strength. There is, of course, a limit as to how light you can make any particular article without sacrificing the durability of the unit using the same material.
Weight is an issue in just about every item built. The axiom that ounces equal pounds and pounds equal pain rings true for rucksacks, weapons systems and aircraft. To this end, BCM looked to use alternative material for the KMR handguard, and the result is an extrusion with a blend of 96% magnesium and 4% aluminum.
Pure magnesium is very rigid but also brittle. The addition of aluminum makes the KMR more malleable. Its strength is equal to that of 6061T6, but with one-third less weight. As an example, a quality seven-inch quad rail that I have weighs 11.3 ounces.
Weights of the currently available KMRs are:
- 15 inch: 6.0 ounces
- 13 inch: 5.0 ounces
- 10 inch: 4.25 ounces
- 9 inch: 3.7 ounces
The barrel nut and mounting hardware for each rail weigh 2.2 ounces.
The concern about magnesium has been flammability, but the aluminum blend reduces that to the point where, if exposed to sufficient heat, it would puddle before it ignited. It would be too hot to hold long before that.
KMR 13 weighs five ounces. Barrel nut and mounting hardware weigh another 2.5 ounces. Weight and configuration make this a very shootable gun. Number 125 is a student loaner gun, and as of this writing has 12,400 rounds downrange.
THE HEAT ISSUE
The coating for the handguard was another issue waiting for a solution. It is not possible to anodize magnesium, so the engineers located a proprietary two-step plating process that is stronger than anodizing. The basecoat is a ceramic-like surface that reduces wear and corrosion, and a topcoat adds lubricity and eliminates reflective IR signature.
As the side of the rail is 1.5 inches from the barrel, you can expect it to get warm when engaged in a harsh firing schedule. Heat is generated each and every time you press the trigger, and the more you shoot, the hotter the front end will get. I use rail panels near the vicinity of the vertical foregrip on the bottom and support side to mitigate the heat. I leave the rest of the rail uncovered to promote cooling.
I have been running five KMR guns: three KMR-13, one KMR-10 and one KMR-9. I have been using one of the KMR-13s for over a year, and as of this writing it has 12,500 rounds through it. Subjectively, losing weight on the front of the gun makes it easier for me to drive it. The combination of the KMR and the Extreme Light Weight barrel seem to work better for me than any other AR I have used, but again, it is subjective. I have seen no issues with any of the KMRs.
Ethan Johns’ KMR 13, showing the barrel attachment hardware.
WHY ANOTHER RAIL SYSTEM?
Why is there a KeyMod Rail? With the number of different rail systems out there, why another one? Some people are reluctant to accept change, and others will buy anything that is new. When the first Quad Rails came into existence in the mid-1990s, a great many people understood the utility and flocked to them. Another group of people derided them as being “tacticool” and unnecessary to their needs.
For those whose business it was to hunt other men, the ability to standardize on a system that would allow for the attachment of mission-critical items was apparent. When tubular handguards came onto the scene, things worked out exactly the same. Some loved them, some despised them, and some decided they didn’t need them. The tubular handguards permitted a clean, lighter-weight unit, and the ability to have Pic Rail sections only where needed was a major selling point.
Others wanted a simpler plastic handguard that still had the ability to have a light and/or vertical foregrip mounted, and these came into being (such as the Magpul MOE). They also required an interface in order to mount equipment to the rail, but this system is significantly less expensive.
About the only thing that has remained standard is the MIL-STD-1913 rail. It has proven its worth and, as a platform for accepting return-to-zero (RTZ) mounts and having a degree of flexibility, it remains king of the hill. It is also unnecessary for attachments that do not require an RTZ, such as weapon-mounted white lights, vertical foregips, hand stops and the like. None of the handguards will forsake the MIL-STD-1913 rail for those sights that need a solid RTZ capability.
There are literally millions of accessories and an untold number of weapons systems, and to consider replacing them with something that may not be as capable is pure madness.
CHOOSE CAREFULLY
Understand that the mission drives the gear train. Before you make any purchase, consider why you are doing it. If you are a dabbler, dabble on. If you have disposable income, go with whatever you want. If this is a professional issue, consider carefully what best fits your needs. There are likely a great number of choices available to you, so due diligence is required.
If you base your purchase purely on initial price, you are looking at Airsoft or offshore manufacturers. The serviceability of these items is always in question, and I have seen multiple issues with durability in class.
Conversely, many have told me that they have had these “just as good as” items for years without a problem. And they are telling the truth, because they use those guns only when Haley’s Comet passes by the Earth.
The KeyMod Rail does not duplicate or replace the Pic Rail. It is a lighter, less bulky unit that provides the ability to rapidly reconfigure the weapon to mission requirements. And it does it very well.
Pat Rogers is a retired Chief Warrant Officer of Marines and a retired NYPD Sergeant. Pat is the owner of E.A.G. Inc., which provides services to governmental organizations and private citizens. He can be reached at [email protected].
SOURCE:
Bravo Company Mfg.
(877) 272-8626
www.bravocompanymfg.com